Yeast maker improves efficiency with tech upgrades
2024-11-12 14:11:10
By Yan Wanqin. Yang Chunyan, Li Rong also contributed to this article.
Angel Yeast (Yichang) Co., Ltd., the world’s second-largest yeast producer, has been implementing projects to upgrade technology, enhance efficiency, and reduce costs.
Through its heat recycling project, Angel Yeast could save 3,000 tons of hot steam gas, and cut costs by more than 700,000 yuan (US$97,447) annually.
The factory’s water recycle project also reduced water usage by 1,800 tons each year. “We optimized the production process and collected the water from yeast separators and centrifuges. Now the hot water is collected and used to mix with sugar, while the cold water is used to wash tanks," said Zhang Zhiliang, a technical worker at the company.
Frontline workers are continuously studying similar technical optimizations to enhance efficiency. Each month, the yeast production workshop undergoes three to four technical upgrades aimed at reducing costs and increasing productivity, Zhang added.
Angel Yeast (Yichang) is the first company to establish operations in the Hubei Synthetic Biology Industrial Park. Its production lines have been upgraded for high levels of automation, intelligent operation, and digital integration. Alongside leading in production capacity, its green recycling and circular production patterns have become industry benchmarks.
In Angel Yeast's production workshop, intelligent robots shuttle materials to designated locations after receiving instructions.
The factory features automated guided vehicles, 13 robots, and four automated production lines.
Using advanced technologies, the highly concentrated wastewater from yeast production is converted into yeast metabolites, which serve as a raw material for producing organic fertilizers.
This year, the company has completed 37 technological upgrades and 2,906 minor improvements, achieving a yeast output of 19,800 tons.
Angel Yeast (Yichang) Co., Ltd., the world’s second-largest yeast producer, has been implementing projects to upgrade technology, enhance efficiency, and reduce costs.
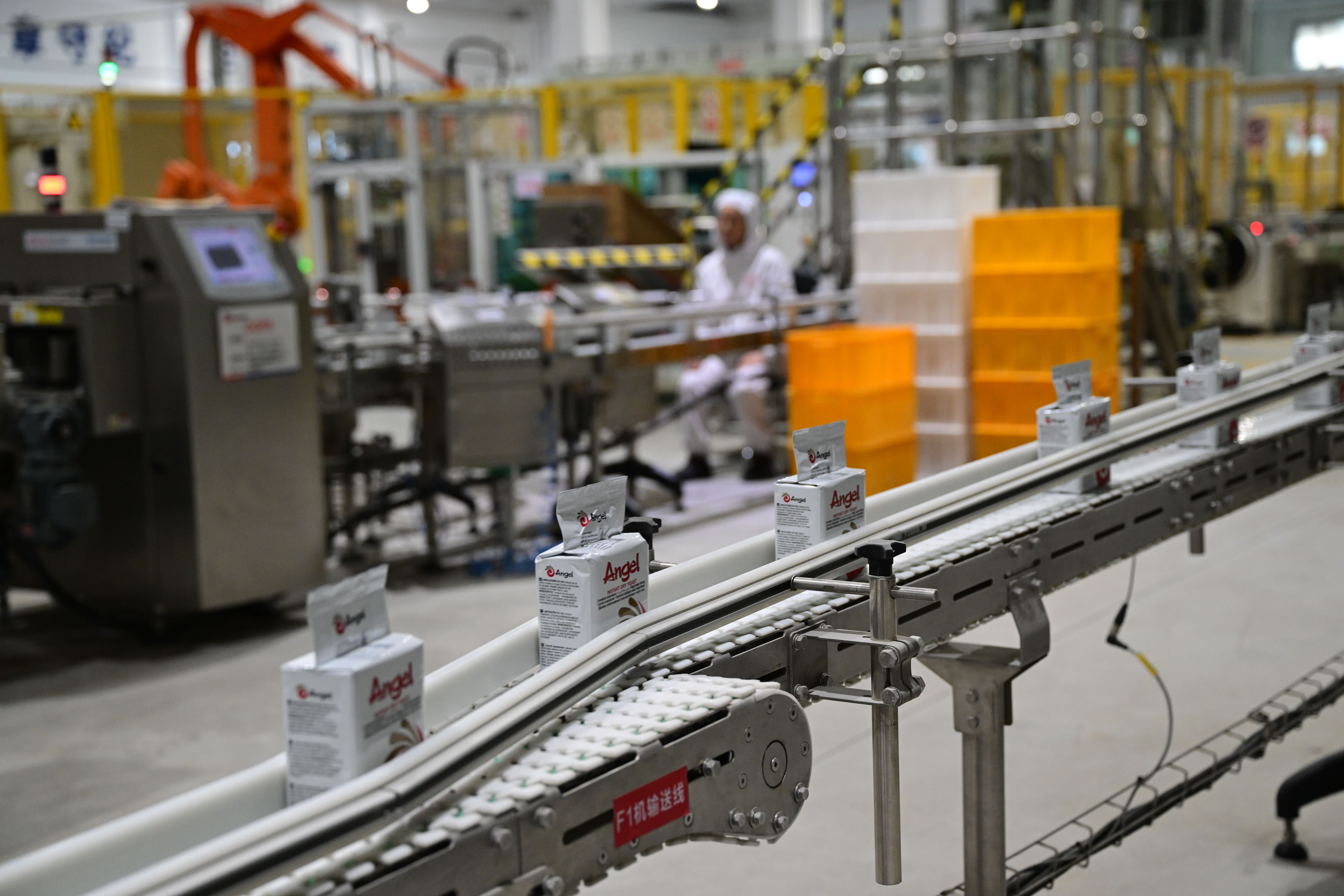
Packaging workshop at Angel Yeast (Yichang) Co., Ltd. Photo by Liu Kang.
Through its heat recycling project, Angel Yeast could save 3,000 tons of hot steam gas, and cut costs by more than 700,000 yuan (US$97,447) annually.
The factory’s water recycle project also reduced water usage by 1,800 tons each year. “We optimized the production process and collected the water from yeast separators and centrifuges. Now the hot water is collected and used to mix with sugar, while the cold water is used to wash tanks," said Zhang Zhiliang, a technical worker at the company.
Frontline workers are continuously studying similar technical optimizations to enhance efficiency. Each month, the yeast production workshop undergoes three to four technical upgrades aimed at reducing costs and increasing productivity, Zhang added.
Angel Yeast (Yichang) is the first company to establish operations in the Hubei Synthetic Biology Industrial Park. Its production lines have been upgraded for high levels of automation, intelligent operation, and digital integration. Alongside leading in production capacity, its green recycling and circular production patterns have become industry benchmarks.
In Angel Yeast's production workshop, intelligent robots shuttle materials to designated locations after receiving instructions.
The factory features automated guided vehicles, 13 robots, and four automated production lines.
Using advanced technologies, the highly concentrated wastewater from yeast production is converted into yeast metabolites, which serve as a raw material for producing organic fertilizers.
This year, the company has completed 37 technological upgrades and 2,906 minor improvements, achieving a yeast output of 19,800 tons.